Mold maintenance and repair is one of the key factors to ensure smooth production. Especially for the production of common items in daily life such as coffee cup LIDS, the design and functionality of the mold directly affect the production efficiency and product quality. The independent core design of the 12CAV coffee cup lid mould not only optimizes the molding process of the product, but also greatly simplifies the later maintenance and repair work of the cup mould, improves the maintenance efficiency and reduces the production cost.
The main advantage of the standalone kernel design is its modular nature, which makes maintenance and repair tasks extremely easy. When any kernel in the 12CAV coffee cup lid mould needs maintenance or repair, the staff can easily access and operate only on that specific kernel, which greatly saves time and labor. Because the cores are independent, they can be interchanged between different molds, which means that if one core is under maintenance while the other is still working, production can continue, reducing downtime for the machine.
Another advantage of this design is that it reduces interference with the entire production line. In a traditional monolithic cup mold design, a small repair may require a long downtime, while the 12CAV coffee cup lid mould avoids this situation. Maintenance teams are able to quickly replace damaged cores while other parts remain unchanged, ensuring continuous operation and high production.
The independent core design of the 12CAV coffee cup lid mould
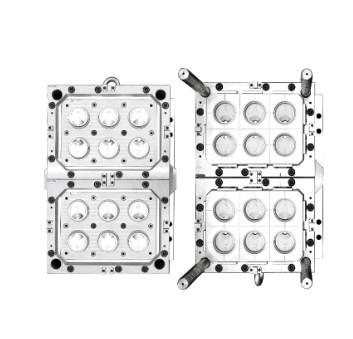